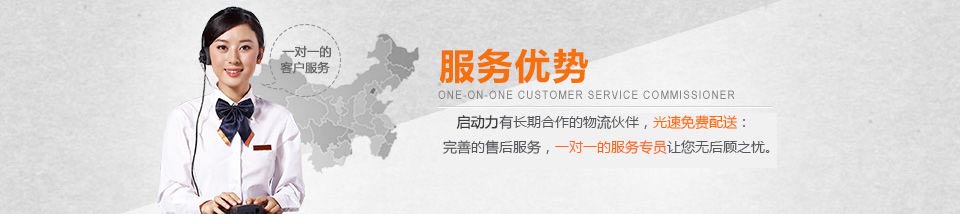
提高数控铣床生产效率的方法
数控铣床是综合应用计算机、自动控制、自动检测及精密机械等高新技术的机电一体化产品。一台数控铣床的价格少则几十万,多则几百万,而许多数控铣床的加工能力得不到充分的体现,发挥不出其最佳作用。据调查,数控铣床的实际切削时间不到工作时间的55% ,造成极大的浪费。而影响数控铣床加工效率的因素很多,也很复杂。笔者在数控的教学实践和对企业的调查中发现:影响数控铣床生产效率的因素是多种多样的。现在许多学校、企业对此重视程度不够,使数控铣床的生产效率大大降低。事实上,数控铣床生产效率可以提升的空间是很大的。在使用过程中,只有充分考虑到影响生产效率的各方面因素并想方设法地提高生产效率,才能使数控铣床的生产能力得到充分的发挥。
1 制订合理的加工路线,减少数控铣削的辅助时间为了提高数控铣床的生产效率,首先必须认真分析数控铣床所加工的零件,弄清零件的材料、结构特点和精度、粗糙度、热处理等方面的技术要求。然后在此基础上,选择合理地铣削加工方式和简捷地加工路线。加工方式的选择:数控铣削的加工方式可分为顺铣与逆铣两种。因为数控铣床的机械传动系统和结构本身就有较高的精度和刚度,相对运动面的摩擦系数小,传动部件的间隙小,运动惯量小,并有适当的阻尼比,所以可以采用顺铣的方式加工,以提高数控铣床的加工效率。加工路线的确定:正确简捷地加工路线,是保证加工质量和提高效率的基础。选择零件的加工路线时,必须遵守加工路线的确定原则,才能达到提高生产效率的目的。确定加工路线的原则主要有:应能保证零件的加工精度和表面粗糙度的要求,且效率较高;应尽量使加工路线最短,这样既可减少程序段,又可减少刀具空程走刀时间;应使数值计算简单,程序段数量少,以减少编程工作量。此外,确定加工路线时,还要考虑工件的加工余量和机床、刀具的刚度等情况,确定是一次走刀,还是多次走刀来完成加工。同时,应尽量做到一次装夹、多方位加工,一次加工成形。这样,可减少工件的安装次数,有效缩短搬运和装夹的时间。这样,既能有效地提高加工效率又能很好地保证零件的位置精度要求。
2 选择恰当的刀具,提高数控铣床的切削效率选择刀具应考虑数控铣床的加工能力、工序内容、工件材
料等因素。数控铣床所选择的刀具,不仅要求精度高、刚度好、耐用度高,而且要求尺寸稳定、安装调整方便。所以应采用新型优质材料制造数控加工刀具,并优化刀具参数,使刀具的尺寸
与被加工工件的表面尺寸和形状相适应。那么,怎样选择数控铣床的切削刀具呢?
2.1 选择性能好的刀具
在数控铣床的切削加工中,金属切削刀具的作用是极其重要的。制造刀具的材料必须具有很高的高温硬度和耐磨性,以及必要的抗弯强度、冲击韧性和化学惰性,还要有良好的工艺性,且不易变形。同时,刀具切削部分的几何参数对切削效率的高低和加工质量有很大影响。为防止刀尖处的热磨损,主、副切削刃连接处应采用修圆刀尖或倒角刀尖,以增大局部刀尖角,增大刀尖附近切削刃的长度和刀具材料的体积,以提高刀具刚性和减少刀具破损率。此外,刀具如果没有储备,或储备数量太少,很快就用完了,而新刀具一时又买不到,这样必然会影响数控铣削加工的效率。所以,合理的刀具储备也可以达到提高数控铣床的生产效率的目的。
2.2 合理确定对刀点
对刀点是在数控机床上加工零件时,刀具相对于工件运动的起点。又称“程序起点”或“起刀点”。对刀点的选择必须遵守以下原则:
(1)便于用数字处理和简化程序编制;
(2)在机床上找正容易,加工中便于检查;
(3)引起的加工误差小。
对刀点的位置可选在工件上,也可选在工件外面(如夹具或机床上),但必须与零件的定位基准有一定的尺寸关系。对刀点应尽量选在零件的设计基准或工艺基准上,如以孔定位的工件,可选孔的中心作为对刀点。刀具的位置则以此孔来找正,使“刀位点”与“对刀点”重合。这样,可以便可以更好地提高对刀的效率,保证加工质量。
3 合理安装夹紧工件,提高装夹速度
在数控铣床上加工工件时,工件的定位安装应力求使设计基准、工艺基准与编程计算的基准统一;尽量减少装夹次数,尽可能在一次定位装夹后,加工出全部待加工表面;避免采用占机人工调整式加工方案,以充分发挥数控铣床的效能。数控铣床切削加工时,在对零件进行定位、夹紧设计以及夹具的选用等问题上要作全面考虑。在设计选择夹具时,首先要保证夹具的坐标方向与机床的坐标方向相对固定。其次,要
协调零件和机床坐标系的尺寸关系。同时,还应考虑:
(1)当零件生产批量不大时,应尽量采用组合夹具、可调式夹具及通用夹具,以缩短生产准备时间、节省生产费用;
(2)在成批生产时才考虑采用专用夹具,并力求结构简单;
(3)零件的装卸要快速、方便、可靠,以缩短机床的停机时间;
(4)夹具上各零部件应不妨碍机床对零件各表面的加工;
(5)在选择工装时应有利于刀具交换,避免发生干涉碰撞;
(6)在成批生产中还可采用多位、多件夹具,以提高加工效率。
4 合理选择切削用量,提高加工余量的切除效率
切削用量包括:主轴转速(切削速度)、背吃刀量、进给量。在选择数控铣床的切削用量时,如果是粗加工,一般以提高生产率为主,但也要考虑经济性和加工成本;要是半精加工和精加工,应在保证加工质量的前提下,兼顾效率、经济性和加工成本。具体数值应根据机床说明书、切前用量手册,并结合经验而定。在选择合理切削用量的同时,提高零件毛坯的制造质量也能降低切削表面轨迹形成的残留高度,改善表面粗糙度,从而有利于提高切削质量和生产效率。
5 实行刀具预调和自动测量,减少占机调整时间数控铣削加工过程中往往要用到多把不同的刀具,如果刀具不能预先调好,就需要将数控铣床当作预调器,操作者把每一把刀具都安装到主轴上,慢慢地确定它们的准确长度和直径。然后,通过CN C 控制面板上的按键用人工输入。如果使用刀具预调器,它可以直接把计算机刀具存储系统与机床自动连接起来,下载偏置数据,节省了时间,消除了数控输入差错,大大提高数控铣床的生产效率。而在数控铣床采用自动测量装置,精密的检测仪等测量装置。采用自动测量装置时,操作员无须对零件的定位保证非常精准,也不需要操作员时刻移动和调节零件以配合加工程序的某些固定坐标系,可以减少装夹时间,降低加工误差。这样也能提高数控铣床的生产效率。
6 正确维护保养,延长数控机床的平均无故障时间
数控铣床是机械、电气、液压、气动、计算机技术、控制技术、检测与测量技术、电力拖动技术、PLC 等集于一身的技术密集型产品。使用者平时正确的维护保养,及时的故障排除和及时的修理,是可延长各种元器件、数控系统和各种装置的使用寿命和预防意外事故的发生,是充分发挥机床性能和长时间稳定工作的基本保证。因此,应建立完善的日常维护保养制度,严格按规定对数控铣床进行日常检查、周检查、月检查、半年检查。尽量少开或不开数控柜及其他各电气控制柜门,保持散热通风系统正常工作。而且,在使用过程中出现的各种报警应及时排除。只有这样,才能延长数控铣床的无故障时间,提高数控铣床的使用效率。
7 加强信息化建设和人员培训,提高数控铣床的使用效率
在生产实践中,数控铣床的加工效率在很大程度上取决于切削时间占数控铣床工作时间的比例,这个比值越大,生产效率也就越高。因此, 应加强信息化建设, 充分利用CA D /CA M /CA E/CA PP 技术和网络技术,做到产品设计、工艺信息资源共享,采用合理的CA M 编程策略,设计合理的刀具轨迹,形成优化合理的数控加工程序并直接通过网络输送到数控铣床。这样可以大大减少占机调整时间和人工录入程序、调试程序的时间,提高数控铣床的使用效率。同时,数控铣床的科技含量越来越高,对人员的素质要求也越来越高。而在实际生产中,由于人员技术水平低,操作不熟练,用在程序调试、加工中换工件等非加工状态的时间过长,致使数控铣床加工效率低下。因此,加强对技术人员、操作人员和维修人员的培训,提高他们的技术水平与操作技能,就能间接地提高数控铣床的使用效率。
实践证明,在数控铣床的实际应用中,只要我们能充分了解数控铣床及其所加工的零件的特点,通过采取制订合理的加工路线,减少数控铣削的辅助时间;选择恰当的刀具,提高数控铣床的切削效率;合理安装夹紧工件,提高装夹速度;合理选择切削用量,提高加工余量的切除效率;实行刀具预调和自动测量,减少占机调整时间;正确维护保养机床,延长数控机床的平均无故障时间;加强信息化建设和人员培训,提高数控铣床的使用效率等六个方面,就能大大地提高数控铣床的生产效率,充分发挥数控铣床的效能。
下一篇:装配铣床夹具需要注意的事项 上一篇:数控铣床的主要功能
最新资讯
- 应用平面数控钻床进行镜面磨削的N个技巧
- 下一个风口?数控钻床金属加工行业的这些趋势值得注意
- 数控钻床做机加工到底能不能带手套呢?
- 什么是高档数控机床?
- 我国工业机器人行业会不会重复数控机床行业的悲剧?
- 如何看待我国数控机床行业?
- 启动力教你怎么着手学习数控钻床?
- 启动力数控机床讲解最全的数控钻床分类说明
- 温岭这家公司收购德国百年企业 还参与奔驰宝马制造
- 香河机器人小镇上演“机器人总动员”
最新产品
- QDLPD6025型大型数控钻床
- PD1040型数控钻铣床
- QDLPD2525型数控铣床
- PD2016型龙门数控钻床
- 小型PD1010型数控钻床
- QDLPD2020型高速数控钻床
- QDLPD3060型高精度数控钻床
- PD1016型数控钻铣床