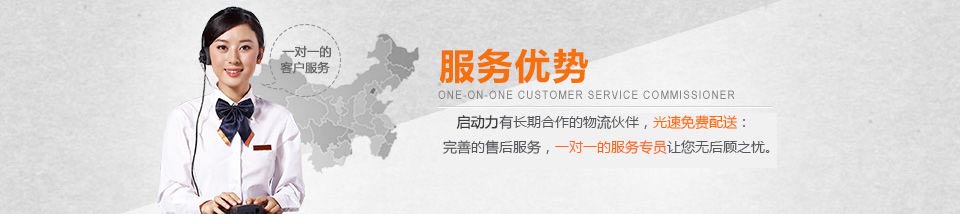
高精密和超精密机床的区别
随着航空航天、汽车等工业的技术发展和环保要求的不断提高,对零件的加工精度和工艺要求也越来越高。以满足欧盟Ⅴ尾气排放要求的柴油发动机为例,燃油喷射阀门(图1)需要在每一冲程内快速开闭5~8次,而阀门往复行程仅20μm,对阀门的气密性和动态特性的要求很高,从而对其加工精度的要求也大大提高。
高精度加工机床是对应上述加工要求的机床。高精密加工的精密度级别介乎精密加工与超精密加工之间,如表1所示。
高精度机床的结构特点
为了实现较高精度的切削运动,高精密加工机床的运动控制普遍采用较高级别的功能部件。
在导轨和轴承方面,由于高精度加工需要实现高精度和平稳的定位运动、轨迹运动和微小距离运动,因此高精度加工机床采用静压丝杠和静压导轨较为常见。此外,高精密加工机床的电主轴也可采取动压或静压轴承的方案,以同时实现支承和冷却功能,并提高主轴的刚度和阻尼性能。
在位置控制方面,由于精密测量是控制高精度加工的前提,要保证机床的运动达到需要的精度级别,其电子尺的测量精度须要高1~2个数量级。目前高精度加工机床一般采用分辨率达0.05~0.1μm的玻璃光栅。
机床的加工精度、光洁度和刀具寿命与机床的刚性成正比,因此高精度加工机床尤其重视床身的设计和材料选择。
以瑞士DIXI公司的JIG系列坐标镗床为例,其床身材料为球墨铸铁,经过有限元分析优化后,床身的静态刚度达120N/μm,比一般数控机床高3倍,高频动态刚度比一般机床高2~3倍。此外,JIG系列机床的床身采用三点支撑,并将刀库、电气柜、托盘交换装置等周边系统与床身分离,此举除可以简化机床安装以外,还有提高机床稳定性、降低床身颤动的作用。
提高机床刚性的另一种途径是使用人造花岗石材料浇注的床身。以德国KERN公司的Pyramid Nano机床为例,该机床采用了KERN公司专有的Armorith人造花岗石材料(图2中灰色表示Armorith人造花岗石材料,蓝色表示金属部件),与球墨铸铁相比,Armorith材料的阻尼性能高10倍,热导率低50%,热膨胀系数也较低。稳定的温度及震动阻尼基座使Pyramid Nano机床可以加工出光洁度非常高的表面。此外,Armorith材料具有非常高的密度,2t重的机身仅占2.5m2车间面积。
机床运行时产生的热量所造成的热变形对加工精度会产生巨大的影响。超精密机床由于机床的总质量远高于所切削的材料,而且单位时间的切削量少,因此,只需要维持机床所处环境的温度恒定,即可避免热变形的问题。可是,高精度机床的使用条件是中批量和大批量生产,要求高速度、大切削量的加工,机床的工件、刀具、丝杠、主轴等部件在加工过程中将产生可观的热量,必须在机床设计上加以周密考虑。
以DIXI的JIG系列坐标镗床为例,为了控制热变形,在机床7处主要热源设置了温度控制点, 其分布如图3所示。
同时在各个热源都设计了独立的冷却循环回路并计算好各处热源的发热量。在机床工作期间,冷却液循环系统根据各个热源的发热量供应比室温低2℃的冷却液。确保每各个循环回路都提供稍大于热源发热量的冷却量,以保持机床的热变形在允许范围之内。
由于刀具在切削过程中的热变形无法完全避免,机床的数控系统可以对刀具引起的Z轴误差作出补偿。最后,必须指出的是,除了先进功能部件和技术以外,超精密机床的制造也离不开传统工艺,例如,装配1台超精密机床需要高达数百小时的刮研工作量。
超精密加工
超精密加工是指尺寸精度在100nm以内的加工技术。随着航空航天、精密仪器、光学和激光技术的迅速发展,以及人造卫星姿态控制和遥测器件、光刻和硅片加工设备等各种高精度平面、曲面和复杂形状零件的加工需求日益迫切,超精密加工的应用范围日益扩大。它的特点是可以直接加工出具有纳米级表面光洁度和亚微米级形面精度的表面,借以实现各种优化的、高成像质量的光学系统,并促使光学电子设备的小型化、阵列化和集成化。
近年来,超精密加工开始从高技术装备制造领域走向消费品生产领域。应用最为广泛的是各种电子产品中的塑料成像镜头,如手机和数码相机镜头、光盘读取镜头、人工晶体等。同时,也开始用于各种自由曲面光学零件、微透镜阵列、渐进式镜片、菲涅尔透镜、微沟槽阵列等各种光束处理镜片的加工。与成像镜头相比,光束处理器件具有更为复杂的形面。若干典型的光学器件如图4所示。
单晶金刚石车削和法向成型车削
单晶金刚石车削(Single Point DiamondTurning)是最早出现的超精密加工工艺。单晶金刚石刀具是采用单晶金刚石制造的尺寸很小的切削刀具,由于其刀尖半径可以小于0.1μm,工件加工后的表面粗糙度可达纳米级。因此能在硬材料上直接切削出具有极光洁的表面和超高精度的微小三维特征,适用于塑料镜头注塑模模芯、铝合金反射镜以及有机玻璃透镜等零件的加工。美国Moore Nanotechnology System公司的450UPL型超精密车床的外观如图5所示。
为了解决这类光学器件的加工,开发了刀具法向成形(Tool-normalContouring)加工模式。将刀架安装在回转B轴上,机床对X、Z、B轴同时进行控制,使刀具在车削过程中始终保持刀尖与工件曲面的法线重合,一次完成整个镜面的车削,如图6所示。
除了回转对称的镜片外,各种波导器件在产品上的应用也越来越多,波导器件是一种引导和约束光传播路径和方向的光学器件。条形波导器件特点是镜面曲率大、形状狭长,采用一般车削加工的效率低而且加工范围受车床的主轴回转半径限制。飞刀切削(Fly-cutting)是在超精密车床的基础上,通过改变刀具和工件的装夹方法,提高大曲率狭长工件切削效率的加工模式。它的原理是将刀具径向安装在圆柱形的刀盘前端上,再将刀盘安装在车床主轴上随主轴高速旋转,故称为“飞刀”。工件则安装在工作台上随工作台进行直线进给,从而实现切削过程。条形波导器件和飞刀切削过程如图7所示。
刀切削的另一种用途是加工具有微结构阵列的光学器件。微结构表面是指具有特定功能的微小表面拓扑形状,形面精度达亚微米级的表面。如微结构阵列光学器件、菲涅尔透镜、衍射光学元件、梯度折射率透镜、闪耀光栅、多棱镜等,典型的金字塔微结构如图8所示。
慢刀和快刀伺服车削技术
飞刀铣削虽然可以加工部分微结构,但飞刀加工时工件的安装与调整比较困难,加工面形仍然受刀具尺寸的影响。此外,非几何形状的反光罩、正弦相位板等具有自由曲面阵列的光学器件,由于其微结构的排列为非相交线组成,难以采用飞刀切削加工。
慢刀伺服和快刀伺服车削是近年发展比较快的超精密加工技术,这2种技术均能显著提高微结构阵列和自由曲面光学器件的加工效率。
1慢刀伺服车削
慢刀伺服(Slow Tool Servo)车削是对车床主轴与Z 轴均进行控制,使机床主轴变成位置可控的C轴,机床的X、Z、C三轴在空间构成了柱坐标系,同时,高性能和高编程分辨率的数控系统将复杂面形零件的三维笛卡尔坐标转化为极坐标,并对所有运动轴发送插补进给指令,精确协调主轴和刀具的相对运动,实现对复杂面形零件的车削加工。
慢刀伺服车削Z轴和X轴往往同时作正弦往复运动,需要多轴插补联动,如图9所示。
2快刀伺服车削
快刀伺服(Fast ToolServo)车削与慢刀伺服的差别在于:将被加工的复杂形面分解为回转形面和形面上的微结构,然后将两者叠加。
由X轴和Z轴进给实现回转形面的轨迹运动,对车床主轴只进行位置检测并不进行轨迹控制。借助安装在Z轴但独立于车床数控系统之外的冗余运动轴来驱动刀具,完成车削微结构形面所需的Z轴运动。这种加工方法具有高频响、高刚度、高定位精度的特点。
快刀伺服是一套伺服控制的刀架及其控制系统,金刚石刀具在压电陶瓷驱动下可以进行Z轴的往复运动。控制系统在实时采集主轴角度信号的基础上,实时发出控制量,控制刀具实时微进给,从而实现刀具跟踪工件面形的起伏变化,如图10所示。
结束语
随着太空探测、卫星通信和能源技术的发展,超精密加工技术的应用范围正在急剧扩大。例如,具有巨大的产业、经济、科技和社会效应的太阳能利用和半导体照明等战略性新兴产业都离不开超精密加工技术的支撑。因此,超精密加工已成为衡量一个国家制造科技水平的重要标志。
图1 高精度燃油喷射阀门
高精度加工机床是对应上述加工要求的机床。高精密加工的精密度级别介乎精密加工与超精密加工之间,如表1所示。
高精度机床的结构特点
为了实现较高精度的切削运动,高精密加工机床的运动控制普遍采用较高级别的功能部件。
在导轨和轴承方面,由于高精度加工需要实现高精度和平稳的定位运动、轨迹运动和微小距离运动,因此高精度加工机床采用静压丝杠和静压导轨较为常见。此外,高精密加工机床的电主轴也可采取动压或静压轴承的方案,以同时实现支承和冷却功能,并提高主轴的刚度和阻尼性能。
在位置控制方面,由于精密测量是控制高精度加工的前提,要保证机床的运动达到需要的精度级别,其电子尺的测量精度须要高1~2个数量级。目前高精度加工机床一般采用分辨率达0.05~0.1μm的玻璃光栅。
机床的加工精度、光洁度和刀具寿命与机床的刚性成正比,因此高精度加工机床尤其重视床身的设计和材料选择。
以瑞士DIXI公司的JIG系列坐标镗床为例,其床身材料为球墨铸铁,经过有限元分析优化后,床身的静态刚度达120N/μm,比一般数控机床高3倍,高频动态刚度比一般机床高2~3倍。此外,JIG系列机床的床身采用三点支撑,并将刀库、电气柜、托盘交换装置等周边系统与床身分离,此举除可以简化机床安装以外,还有提高机床稳定性、降低床身颤动的作用。
提高机床刚性的另一种途径是使用人造花岗石材料浇注的床身。以德国KERN公司的Pyramid Nano机床为例,该机床采用了KERN公司专有的Armorith人造花岗石材料(图2中灰色表示Armorith人造花岗石材料,蓝色表示金属部件),与球墨铸铁相比,Armorith材料的阻尼性能高10倍,热导率低50%,热膨胀系数也较低。稳定的温度及震动阻尼基座使Pyramid Nano机床可以加工出光洁度非常高的表面。此外,Armorith材料具有非常高的密度,2t重的机身仅占2.5m2车间面积。
机床运行时产生的热量所造成的热变形对加工精度会产生巨大的影响。超精密机床由于机床的总质量远高于所切削的材料,而且单位时间的切削量少,因此,只需要维持机床所处环境的温度恒定,即可避免热变形的问题。可是,高精度机床的使用条件是中批量和大批量生产,要求高速度、大切削量的加工,机床的工件、刀具、丝杠、主轴等部件在加工过程中将产生可观的热量,必须在机床设计上加以周密考虑。
以DIXI的JIG系列坐标镗床为例,为了控制热变形,在机床7处主要热源设置了温度控制点, 其分布如图3所示。
同时在各个热源都设计了独立的冷却循环回路并计算好各处热源的发热量。在机床工作期间,冷却液循环系统根据各个热源的发热量供应比室温低2℃的冷却液。确保每各个循环回路都提供稍大于热源发热量的冷却量,以保持机床的热变形在允许范围之内。
由于刀具在切削过程中的热变形无法完全避免,机床的数控系统可以对刀具引起的Z轴误差作出补偿。最后,必须指出的是,除了先进功能部件和技术以外,超精密机床的制造也离不开传统工艺,例如,装配1台超精密机床需要高达数百小时的刮研工作量。
超精密加工
超精密加工是指尺寸精度在100nm以内的加工技术。随着航空航天、精密仪器、光学和激光技术的迅速发展,以及人造卫星姿态控制和遥测器件、光刻和硅片加工设备等各种高精度平面、曲面和复杂形状零件的加工需求日益迫切,超精密加工的应用范围日益扩大。它的特点是可以直接加工出具有纳米级表面光洁度和亚微米级形面精度的表面,借以实现各种优化的、高成像质量的光学系统,并促使光学电子设备的小型化、阵列化和集成化。
近年来,超精密加工开始从高技术装备制造领域走向消费品生产领域。应用最为广泛的是各种电子产品中的塑料成像镜头,如手机和数码相机镜头、光盘读取镜头、人工晶体等。同时,也开始用于各种自由曲面光学零件、微透镜阵列、渐进式镜片、菲涅尔透镜、微沟槽阵列等各种光束处理镜片的加工。与成像镜头相比,光束处理器件具有更为复杂的形面。若干典型的光学器件如图4所示。
图4 典型的光学零件
单晶金刚石车削和法向成型车削
单晶金刚石车削(Single Point DiamondTurning)是最早出现的超精密加工工艺。单晶金刚石刀具是采用单晶金刚石制造的尺寸很小的切削刀具,由于其刀尖半径可以小于0.1μm,工件加工后的表面粗糙度可达纳米级。因此能在硬材料上直接切削出具有极光洁的表面和超高精度的微小三维特征,适用于塑料镜头注塑模模芯、铝合金反射镜以及有机玻璃透镜等零件的加工。美国Moore Nanotechnology System公司的450UPL型超精密车床的外观如图5所示。
图5 450UPL型超精密车床
为了解决这类光学器件的加工,开发了刀具法向成形(Tool-normalContouring)加工模式。将刀架安装在回转B轴上,机床对X、Z、B轴同时进行控制,使刀具在车削过程中始终保持刀尖与工件曲面的法线重合,一次完成整个镜面的车削,如图6所示。
图6 刀具法向成形车削过程
除了回转对称的镜片外,各种波导器件在产品上的应用也越来越多,波导器件是一种引导和约束光传播路径和方向的光学器件。条形波导器件特点是镜面曲率大、形状狭长,采用一般车削加工的效率低而且加工范围受车床的主轴回转半径限制。飞刀切削(Fly-cutting)是在超精密车床的基础上,通过改变刀具和工件的装夹方法,提高大曲率狭长工件切削效率的加工模式。它的原理是将刀具径向安装在圆柱形的刀盘前端上,再将刀盘安装在车床主轴上随主轴高速旋转,故称为“飞刀”。工件则安装在工作台上随工作台进行直线进给,从而实现切削过程。条形波导器件和飞刀切削过程如图7所示。
图7 条形波导器件和飞刀切削过程
刀切削的另一种用途是加工具有微结构阵列的光学器件。微结构表面是指具有特定功能的微小表面拓扑形状,形面精度达亚微米级的表面。如微结构阵列光学器件、菲涅尔透镜、衍射光学元件、梯度折射率透镜、闪耀光栅、多棱镜等,典型的金字塔微结构如图8所示。
图8 金字塔微结构
慢刀和快刀伺服车削技术
飞刀铣削虽然可以加工部分微结构,但飞刀加工时工件的安装与调整比较困难,加工面形仍然受刀具尺寸的影响。此外,非几何形状的反光罩、正弦相位板等具有自由曲面阵列的光学器件,由于其微结构的排列为非相交线组成,难以采用飞刀切削加工。
慢刀伺服和快刀伺服车削是近年发展比较快的超精密加工技术,这2种技术均能显著提高微结构阵列和自由曲面光学器件的加工效率。
1慢刀伺服车削
慢刀伺服(Slow Tool Servo)车削是对车床主轴与Z 轴均进行控制,使机床主轴变成位置可控的C轴,机床的X、Z、C三轴在空间构成了柱坐标系,同时,高性能和高编程分辨率的数控系统将复杂面形零件的三维笛卡尔坐标转化为极坐标,并对所有运动轴发送插补进给指令,精确协调主轴和刀具的相对运动,实现对复杂面形零件的车削加工。
慢刀伺服车削Z轴和X轴往往同时作正弦往复运动,需要多轴插补联动,如图9所示。
2快刀伺服车削
快刀伺服(Fast ToolServo)车削与慢刀伺服的差别在于:将被加工的复杂形面分解为回转形面和形面上的微结构,然后将两者叠加。
由X轴和Z轴进给实现回转形面的轨迹运动,对车床主轴只进行位置检测并不进行轨迹控制。借助安装在Z轴但独立于车床数控系统之外的冗余运动轴来驱动刀具,完成车削微结构形面所需的Z轴运动。这种加工方法具有高频响、高刚度、高定位精度的特点。
快刀伺服是一套伺服控制的刀架及其控制系统,金刚石刀具在压电陶瓷驱动下可以进行Z轴的往复运动。控制系统在实时采集主轴角度信号的基础上,实时发出控制量,控制刀具实时微进给,从而实现刀具跟踪工件面形的起伏变化,如图10所示。
图10 快刀伺服设备
结束语
随着太空探测、卫星通信和能源技术的发展,超精密加工技术的应用范围正在急剧扩大。例如,具有巨大的产业、经济、科技和社会效应的太阳能利用和半导体照明等战略性新兴产业都离不开超精密加工技术的支撑。因此,超精密加工已成为衡量一个国家制造科技水平的重要标志。
下一篇:数控钻床加工程序编程方法 上一篇:数控机床与传统机床相比的优点
最新资讯
- 应用平面数控钻床进行镜面磨削的N个技巧
- 下一个风口?数控钻床金属加工行业的这些趋势值得注意
- 数控钻床做机加工到底能不能带手套呢?
- 什么是高档数控机床?
- 我国工业机器人行业会不会重复数控机床行业的悲剧?
- 如何看待我国数控机床行业?
- 启动力教你怎么着手学习数控钻床?
- 启动力数控机床讲解最全的数控钻床分类说明
- 温岭这家公司收购德国百年企业 还参与奔驰宝马制造
- 香河机器人小镇上演“机器人总动员”
最新产品
- QDLPD6025型大型数控钻床
- PD1040型数控钻铣床
- QDLPD2525型数控铣床
- PD2016型龙门数控钻床
- 小型PD1010型数控钻床
- QDLPD2020型高速数控钻床
- QDLPD3060型高精度数控钻床
- PD1016型数控钻铣床